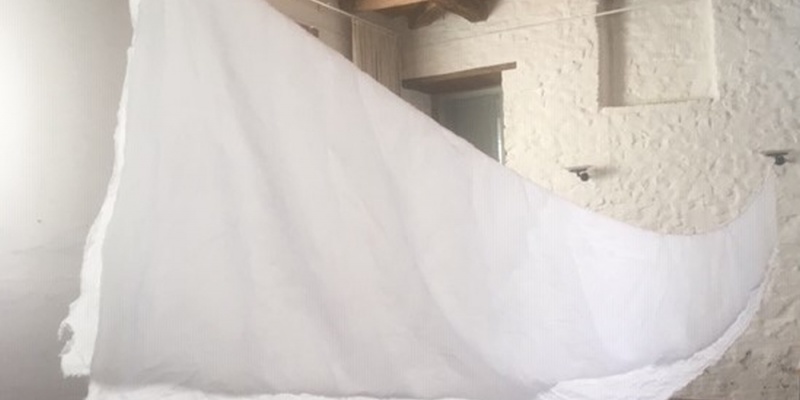
Nachdem die Fäden der neuen Kette für den Jacquardwebstuhl letzte Woche gezwirnt wurden, konnten die Spulen nun aufgesteckt und die neue Kette geschärt werden. Mit der Herstellung der Kette werden Länge, Breite und Dichte des Gewebes sowie die Gewebebindung und das mögliche (Farb-)Muster festgelegt.
Eine Kettschäranlage besteht aus Schärgatter, Gelesewagen und Schärmaschine. Unsere Maschinen stammen aus unterschiedlichen Betrieben und wurden hier als funktionierende Kettschäranlage neu zusammengesetzt.
Vom Schärgatter kommend werden die Fäden durch das Gelese gezogen und auf der Schärmaschine zunächst als schmale Bänder aufgewickelt.
Die Länge der Bänder entspricht der späteren Kettlänge.
Alle nebeneinander auf der Schärtrommel aufgewickelten Bänder ergeben die Breite der Kette. Bei dieser Kette sind es 13 Bänder mit je 105 Fäden von 100 m Länge. Je nach Region wird das „schären“ auch „zetteln“ genannt – ein Blick auf das Schärgatter zeigt, wie schnell man sich hier „verzetteln“ kann.
Im nächsten Schritt müssen die Bänder noch von der Schärtrommel auf den Kettbaum umgewickelt werden.
Über sachkundige Unterstützung freuen wir uns immer ganz besonders. So konnte ein gebrochener Maschinenhebel, der unsere Spinnmaschine außer Betrieb gesetzt hatte, von Richard Möhlenkamp in „Nachbarschaftshilfe“ geschweißt werden. Da es keine Ersatzteile für die inzwischen 97 Jahre alte Maschine mehr gibt, war die Reparatur sehr wichtig. Was erstmal unspektakulär aussieht, erfordert Spezialkenntnisse und Erfahrung. Der von H. Möhlenkamp mitgelieferte „Operationsbericht“ verdeutlicht dies:

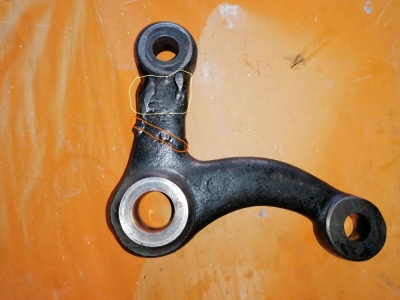
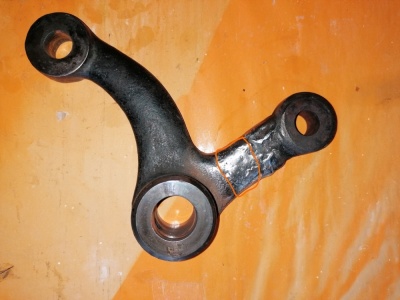
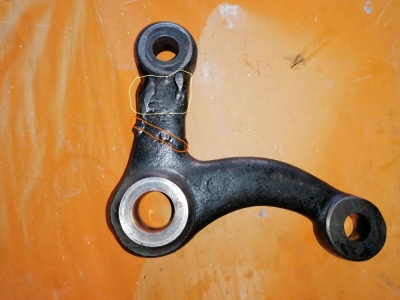
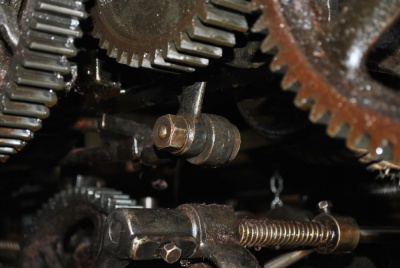
Unser herzliches Dankeschön auch an dieser Stelle an Richard Möhlenkamp!
Am Dienstag wurde unsere Sammel- und Abgabestelle für Stoffe zur Produktion von Behelfsmasken geöffnet (weitere Informationen finden Sie hier). Unsere Techniker waschen die Stoffe. Neben vielen Ehrenamtlichen zuhause produzieren auch unsere Mitarbeiter*innen Masken in verschiedenen Varianten.